相较于传统的金属熔炼和加工工艺,金属粉末烧结板的制造过程能耗较低。在烧结环节,虽然需要对成型坯体进行加热,但由于烧结温度低于金属熔点,且通过优化烧结工艺(如采用快速烧结技术、精细控制加热时间和温度曲线等),能够有效减少能源消耗。同时,在整个生产过程中,由于材料利用率高,减少了因大量废料产生和处理所带来的额外能源消耗,符合节能减排的环保要求,有助于降低工业生产对环境的能源压力。金属粉末烧结板工艺由于实现了近净成形,减少了废料的产生。与传统机械加工过程中产生大量金属切屑等废料不同,该工艺产生的废料主要是少量未烧结完全或不符合质量要求的产品,这些废料可以通过回收和再加工重新利用,降低了对新原材料的需求。此外,在生产过程中,由于不需要进行大规模的熔炼和高温化学反应,避免了传统熔炼工艺中产生的大量有害气体(如二氧化硫、氮氧化物等)和粉尘排放,对环境的污染降低,是一种绿色环保的制造技术。采用微波辅助制备金属粉末,快速合成且改善粉末烧结特性。青海金属粉末烧结板源头供货商
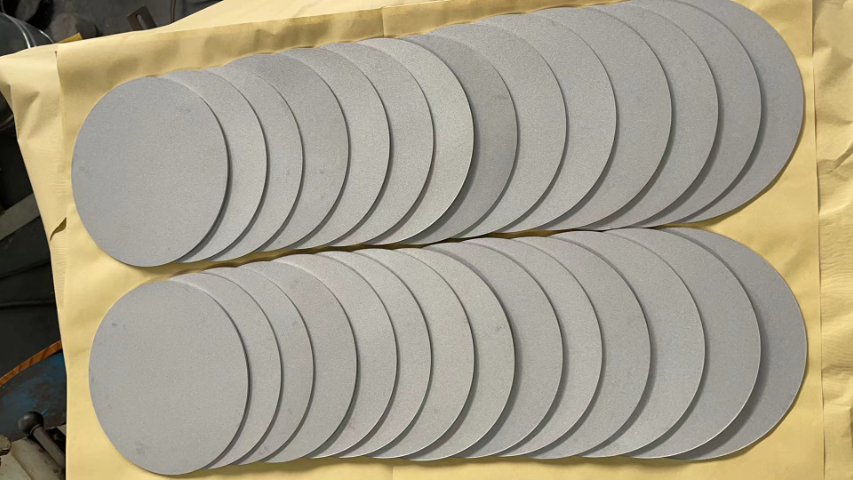
放电等离子烧结技术是在粉末颗粒间施加脉冲电流,利用放电产生的瞬间高温和高压实现粉末快速烧结的方法。SPS技术具有升温速度快(可达100-1000℃/min)、烧结时间短(几分钟到几十分钟)、能有效抑制晶粒长大等优点,适用于制备高性能金属粉末烧结板。在制备纳米晶金属烧结板时,SPS技术能够在极短时间内使纳米粉末颗粒快速烧结,同时保持纳米晶结构。例如,利用SPS技术制备的纳米晶铜烧结板,其硬度比传统粗晶铜烧结板提高了2-3倍,同时保持了良好的导电性和延展性。在制备梯度功能材料烧结板方面,SPS技术也具有独特优势。通过控制烧结过程中的温度、压力和时间等参数,可以在烧结板中形成成分和结构连续变化的梯度层。例如,制备具有耐磨外层和韧性内层的金属梯度烧结板,用于机械零件的表面强化。SPS技术能够精确控制梯度层的厚度和成分变化,提高梯度功能材料的性能和可靠性。青海金属粉末烧结板源头供货商设计梯度成分的金属粉末,使烧结板不同部位呈现不同性能,满足多元需求。
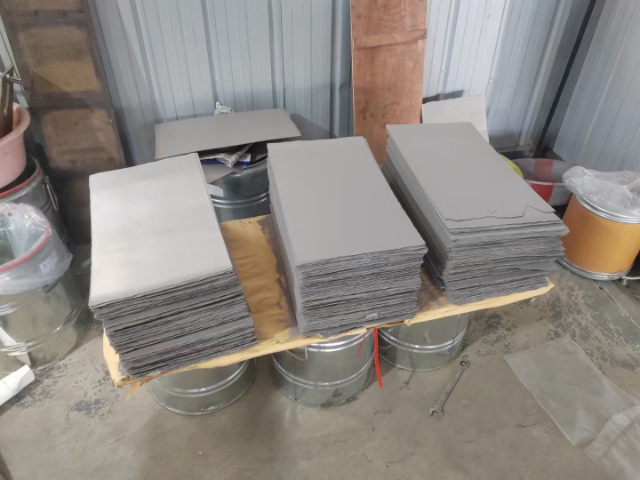
随着纳米技术和微粉制备技术的发展,纳米与亚微米级金属粉末在金属粉末烧结板中的应用逐渐成为研究热点。这些超细粉末具有极大的比表面积和高表面能,能够改善烧结板的性能。在电子封装领域,采用纳米银粉制备的烧结板,由于纳米银颗粒间的烧结驱动力大,在较低温度下就能实现良好的烧结结合,形成高导电、高导热的连接层。与传统微米级银粉烧结板相比,纳米银粉烧结板的电导率可提高 10% - 20%,热导率提高 15% - 25%,有效解决了电子器件散热和信号传输中的关键问题,满足了电子设备小型化、高性能化对封装材料的要求。
钛基粉末以其优异的耐腐蚀性和生物相容性著称,在化工、医疗等领域应用,如化工设备的耐腐蚀部件、人工关节等医疗器械的烧结板制造。镍基粉末特别是在高温合金中,能显著提高材料的高温强度和抗氧化性能,常用于航空发动机高温部件、燃气轮机叶片等烧结板的生产。钨基粉末由于其高熔点和高硬度,常用于制造耐高温、耐磨的烧结板,如在冶金、矿山等恶劣工况下使用的机械部件。粉末质量是决定烧结板性能的关键因素之一。质量的金属粉末应具备高纯度、均匀的粒度分布以及合适的颗粒形状。高纯度的粉末可减少杂质对烧结板性能的负面影响,确保其在物理、化学和力学性能上的稳定性。例如,在电子领域应用的烧结板,若金属粉末中含有杂质,可能会影响其导电性和导热性,进而降低电子设备的性能。研制含金属碳化物的粉末,增强烧结板的高温抗氧化与耐磨性能。
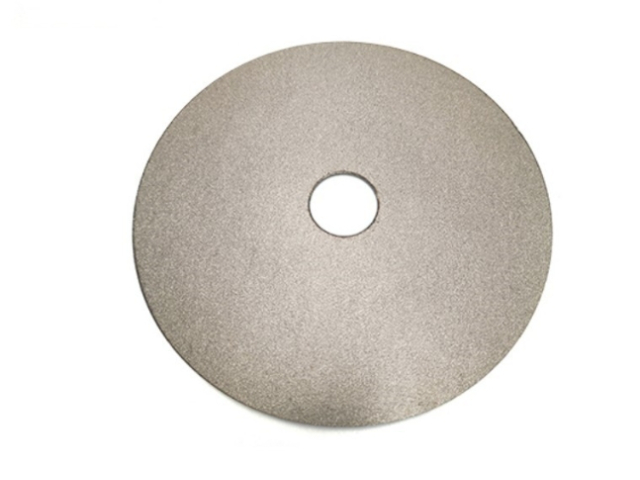
1909年,美国纽约州的库利奇发明拔制电灯钨丝,这一事件极大地推动了粉末冶金的发展。随后在1923年,粉末冶金硬质合金出现,对机械加工领域产生重大影响,也间接促使金属粉末烧结技术得到更多关注和研究。在这一时期,对于金属粉末的制备方法有了更多创新,如机械粉碎法、雾化法、还原法、电解法等逐渐成熟,为获得不同特性的金属粉末提供了可能,进而推动了金属粉末烧结板制造工艺的改进。随着粉末制备技术的进步,烧结工艺也不断优化。人们开始认识到烧结温度、时间、气氛等因素对烧结板性能的重要影响,并进行了大量实验研究。通过控制这些因素,能够在一定程度上提高烧结板的密度、强度等性能,使其应用领域从简单的装饰品制作拓展到一些对材料性能有一定要求的工业领域,如机械零件的制造等。例如,在机械制造中,一些小型的结构件开始采用金属粉末烧结板制造,利用其可加工成复杂形状且材料利用率高的特点,降低生产成本,提高生产效率。开发超疏水表面处理的金属粉末,使烧结板具备防水、防污的特性。青海金属粉末烧结板源头供货商
研发含碳纳米管增强相的金属粉末,大幅提升烧结板力学与导电性能。青海金属粉末烧结板源头供货商
注射成型过程主要包括注射料制备、注射成型、脱脂等步骤。注射料制备时,要确保金属粉末与粘结剂充分混合,形成均匀稳定的混合物。粘结剂的选择和用量对注射料的流动性和成型性能至关重要,过多的粘结剂会导致脱脂困难,且在烧结后可能会留下较多的杂质;过少的粘结剂则无法保证粉末的粘结效果,使注射料的流动性变差。注射成型过程中,注射机的注射压力、注射速度、模具温度等参数需要精确控制,以确保注射料能够顺利填充模具型腔,并形成质量良好的坯体。脱脂是注射成型后的关键步骤,其目的是去除坯体中的粘结剂。脱脂方法有多种,如热脱脂、溶剂脱脂、催化脱脂等。热脱脂是通过加热使粘结剂分解挥发,但加热过程中要控制好升温速率和温度,避免坯体因粘结剂快速分解而产生裂纹或变形。溶剂脱脂则是利用有机溶剂溶解粘结剂,其优点是脱脂速度快,但需要注意溶剂的回收和环保问题。催化脱脂是在催化剂的作用下,加速粘结剂的分解,能够提高脱脂效率和质量。青海金属粉末烧结板源头供货商
文章来源地址: http://yjkc.smdnjgsb.chanpin818.com/jsjgc/jhjc/deta_27800933.html
免责声明: 本页面所展现的信息及其他相关推荐信息,均来源于其对应的用户,本网对此不承担任何保证责任。如涉及作品内容、 版权和其他问题,请及时与本网联系,我们将核实后进行删除,本网站对此声明具有最终解释权。